Why Polyurea is the Best Choice for Secondary Containment and Corrosion Protection in the Oil & Gas Industry
The oil and gas industry operates in some of the harshest environments, where infrastructure is constantly exposed to corrosive chemicals, extreme weather, and heavy industrial wear. Protecting assets like pipelines, tanks, secondary containment and environmental areas is critical to ensuring operational efficiency, environmental compliance, and long-term cost savings.
This is where polyurea coatings stand out. Known for their unmatched durability, chemical resistance, and fast-curing properties, polyurea is the gold standard for protecting oil and gas facilities against corrosion, leaks, and structural degradation.
Let’s explore why polyurea is the best solution for secondary containment and corrosion protection in the oil and gas industry.
1. The Harsh Challenges of the Oil & Gas Industry
The oil and gas sector faces extreme conditions that accelerate wear and deterioration, including:
- Chemical Exposure – Crude oil, refined fuels, and industrial chemicals cause rapid degradation of unprotected surfaces.
- Extreme Weather & Temperature Fluctuations – Equipment and storage tanks must endure intense heat, freezing temperatures, and heavy rainfall.
- High Impact & Abrasion – Machinery, heavy equipment, and constant material movement contribute to wear and tear.
- Environmental & Regulatory Compliance – Stricter regulations require companies to implement effective secondary containment systems to prevent spills and contamination.
Traditional coatings fail under these conditions, leading to premature deterioration, costly repairs, and compliance risks.
2. Why Polyurea is the Best Solution for Secondary Containment
Unlike conventional coatings like epoxy and polyurethane, polyurea offers superior performance in secondary containment applications. Here’s why:
- Chemical Resistance – Polyurea is impervious to oils, fuels, most acids, and industrial solvents, ensuring containment areas remain leak-proof and compliant.
- Seamless & Waterproof Barrier – Unlike traditional coatings that can crack or delaminate over time, polyurea forms a monolithic, seamless membrane that prevents leaks.
- Fast Cure Time – Polyurea sets within seconds and is fully cured quicker than epoxies/urethanes, allowing for quick application and minimal downtime.
- Superior Flexibility & Impact Resistance – It can expand and contract at the same rate of speed as carbon steel without delaminating, remains flexible in cold temperatures, reducing the risk of cracks and failures.
- UV Stability & Longevity – Designed to withstand harsh sunlight and outdoor conditions, polyurea resists fading, chalking, and degradation over time.
For oil and gas companies looking to increase containment reliability, quicker turnaround time and minimize risk, polyurea coatings are the clear choice.
3. Corrosion Protection: Extending the Life of Oil & Gas Infrastructure
Corrosion is one of the costliest issues in the oil and gas industry, leading to equipment failure, pipeline leaks, and environmental hazards. Without proper protection, facilities face:
- High Repair & Replacement Costs – Corroded tanks and pipelines require expensive maintenance and early replacement.
- Safety Hazards – Structural deterioration increases the risk of explosions, leaks, and mechanical failures.
- Regulatory Violations – Non-compliance with EPA and OSHA guidelines can result in hefty fines and legal liabilities.
How Polyurea Prevents Corrosion:
- Creates a Protective Barrier – Polyurea acts as a shield against moisture, chemicals, and abrasive materials, preventing corrosion from forming.
- Superior Adhesion to Metal, Fiberglass & Concrete – It bonds securely to storage tanks, pipelines, and industrial flooring, offering long-term durability.
- Resistance to Rust & Oxidation – Unlike paint-based coatings, polyurea is non-porous, preventing rust from spreading underneath the surface.
For companies looking to maximize asset longevity, polyurea coatings provide a cost-effective and reliable corrosion prevention solution.
4. Real-World Applications of Polyurea in the Oil & Gas Industry
Polyurea is widely used across the oil and gas sector for:
- Pipeline Coatings – Protects underground and above-ground pipelines from corrosion, moisture intrusion, and mechanical damage.
- Storage Tank Linings – Ensures chemical resistance and leak prevention in crude oil, water, and chemical storage tanks.
- Secondary Containment Systems – Provides seamless, chemical-resistant protection to prevent hazardous spills and environmental contamination.
- Concrete & Steel Protection – Shields rig platforms, refineries, and industrial facilities from wear and corrosion.
For oil and gas companies, investing in polyurea means reducing long-term maintenance costs, ensuring safety, and maintaining regulatory compliance.
5. Why ACP is the Trusted Partner for Polyurea Applications
At ACP, we specialize in providing high-performance polyurea coatings tailored to the needs of the oil and gas industry. Our expert application process ensures:
- Precise surface preparation for maximum adhesion and durability.
- Fast and efficient installation to minimize operational downtime.
- Custom solutions designed to withstand industry-specific challenges.
- Long-lasting protection that meets or exceeds industry standards.
From secondary containment to pipeline coatings, ACP delivers reliable, long-lasting protection for oil and gas facilities.
Invest in the Best Protection for Your Facility
In the oil and gas industry, cutting corners on protective coatings can lead to expensive failures. Polyurea offers unparalleled performance, durability, and chemical resistance, making it the ideal solution for secondary containment and corrosion protection. Don’t wait for infrastructure failure to take action—protect your assets today with ACP’s expert-applied polyurea coatings.
Contact ACP today for a consultation and learn how polyurea can safeguard your oil and gas operations for years to come.
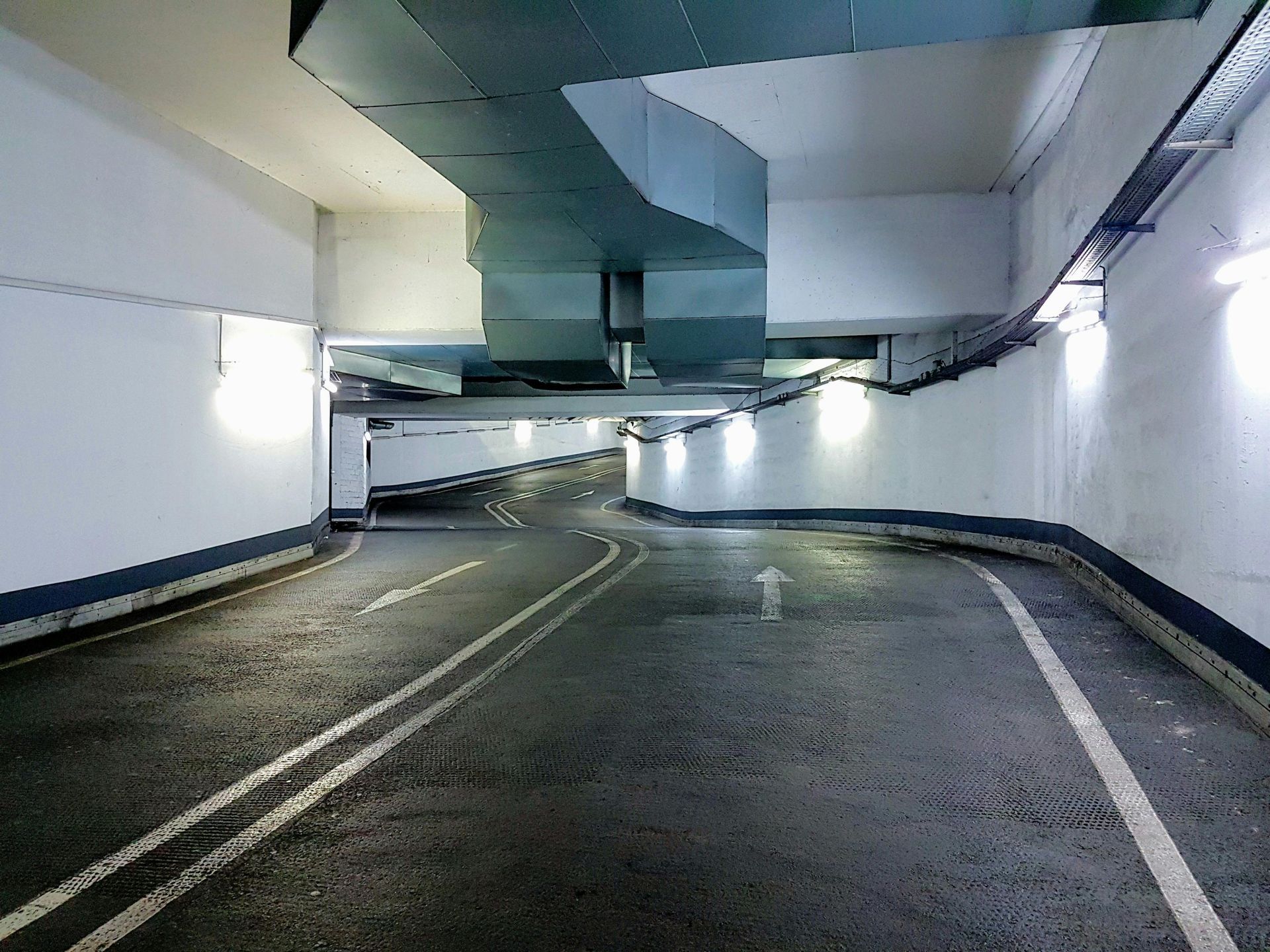