The Role of Cementitious Urethane in Commercial Kitchens
Using the wrong flooring can lead to slip hazards, bacterial growth, cracks, and costly repairs—all of which put employees, food safety, and your business at risk.
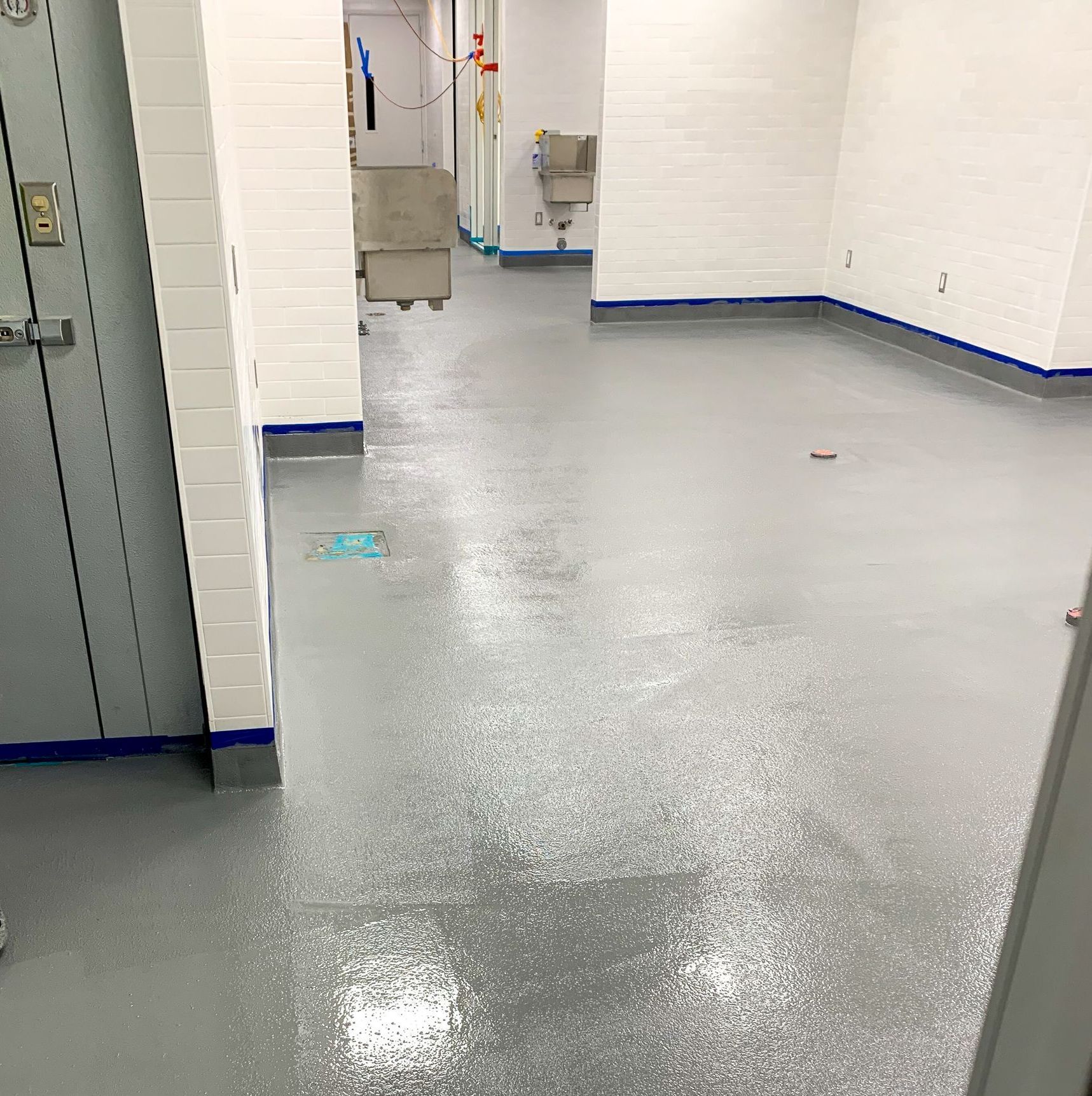
In a commercial kitchen, the flooring is more than just a surface—it’s a critical foundation for safety, hygiene, and efficiency. Whether it’s a restaurant, hotel, cafeteria, or food prep facility, floors in commercial kitchens must withstand constant foot traffic, high heat, oil spills, and daily washdowns.
That’s why cementitious urethane is a leading choice for commercial kitchen flooring. Designed for extreme durability, slip resistance, and hygiene compliance, cementitious urethane is a proven solution that helps kitchens stay safe, compliant, and low-maintenance.
Why Commercial Kitchens Need Specialized Flooring
The fast-paced nature of a commercial kitchen requires flooring that can handle constant stress without failing. Some of the biggest challenges include:
- Extreme Heat & Thermal Shock – Flooring in kitchens must handle temperature swings from freezers (-10°F) to hot ovens (500°F+). Some materials may crack under these extreme changes.
- Constant Moisture & Cleaning Chemicals – Kitchens require daily washdowns, making water absorption a major issue for flooring that isn’t properly sealed.
- Grease & Oil Spills – Slippery floors increase the risk of employee injuries and liability claims.
- Hygiene & Food Safety Compliance – The FDA, USDA, and local health codes require seamless flooring that prevents bacterial buildup and meets sanitation standards. This is not accurate as many commercial kitchens use Quarry Tile for their flooring.
**Pro Tip: If your kitchen floors crack, become slippery, or show signs of wear, they may not meet safety or health code requirements, putting your business at risk of fines or shutdowns.
What is Cementitious Urethane?
Cementitious urethane is a seamless, high-performance flooring system designed for environments with heavy foot traffic, moisture, extreme temperatures, and chemical exposure. It offers:
- Withstands Thermal Shock – Handles rapid temperature changes without cracking.
- Resists Moisture & Spills – Prevents water, grease, and cleaning chemicals from penetrating the surface.
- Seamless & Hygienic – Eliminates grout lines and cracks where bacteria and mold can grow.
- Slip-Resistant – Delivers excellent traction in wet, greasy, or high-risk environments. Cementitious urethane can be engineered to meet or exceed OSHA recommendations and ANSI A326.3 standards with a dynamic coefficient of friction (DCOF) ≥ 0.42 when broadcast with anti-slip aggregate—helping reduce the risk of slips and falls in commercial settings.
- Long-Lasting Durability – Outperforms tile and untreated concrete in commercial kitchen environments.
**Pro Tip: Cementitious urethane is a great option for kitchens because it resists thermal shock, moisture, and grease infiltration, ensuring a longer-lasting, safer surface.
Key Benefits of Cementitious Urethane for Commercial Kitchens
1. High Durability & Resistance to Heavy Traffic
Kitchen floors endure constant movement—from chefs and servers to carts and heavy equipment. Cementitious urethane is designed to:
- Resist wear, impact, and abrasion.
- Handle hot liquids, dropped utensils, and constant movement.
- Last 10+ years with proper care.
2. Health & Safety Compliance
- Meets FDA, USDA, & Local Health Codes for food safety.
- HACCP (Hazard Analysis Critical Control Point) compliant, preventing contamination risks.
- Seamless surface prevents mold, bacteria, and dirt buildup.
3. Superior Slip Resistance for Worker Safety
Slippery kitchen floors are a leading cause of employee injuries and workers’ compensation claims. Cementitious urethane can be customized with slip-resistant additives to:
- Improve traction in wet or greasy areas.
- Reduce liability risks for businesses.
- Keep employees safe and prevent lost workdays due to falls.
4. Waterproof & Chemical Resistant
- Prevents water absorption, reducing damage from daily washdowns.
- Resists grease, cleaning chemicals, and food acids (vinegar, citrus, tomato sauces, etc.).
- Protects concrete from moisture infiltration that leads to cracks and deterioration.
5. Easy to Clean & Maintain
A clean kitchen is a safe kitchen. Cementitious urethane is:
- Seamless & grout-free, making it easier to sanitize than tile.
- Low-maintenance, requiring only standard cleaning methods.
- Resistant to food stains, odors, and microbial growth.
Cementitious Urethane vs. Other Flooring Options
Flooring Type | Chemical Resistance | Thermal Shock Resistance | Durability | Slip Resistance | Maintenance |
---|---|---|---|---|---|
Cementitious Urethane | ✅ Excellent | ✅ Withstands extreme heat/cold | ✅ Long-lasting | ✅ Textured for safety | ✅ Low |
Tile | ⚠️ Stain-resistant | ❌ Can crack in heat/cold | ❌ Grout lines degrade | ❌ Slippery when wet | ❌ High (grout cleaning) |
Unsealed Concrete | ❌ Absorbs chemicals | ❌ Prone to cracking | ❌ Wears down quickly | ❌ Slippery when wet | ❌ High |
**Pro Tip: Tile and untreated concrete may seem cost-effective upfront, but cementitious urethane provides the best long-term value, saving businesses money on repairs, maintenance, and safety claims.
Why ACP is the Trusted Partner for Commercial Kitchen Flooring
At ACP, we understand the unique challenges that commercial kitchens face. Our cementitious urethane flooring solutions provide:
- Seamless application for maximum hygiene.
- Fast turnaround times to minimize business disruptions.
- Slip-resistant, durable, and easy-to-clean surfaces.
- Compliance with industry safety standards to pass inspections.
From restaurants and hotels to industrial kitchens and food service operations, ACP delivers tailored flooring solutions that keep kitchens safe, compliant, and efficient.
Invest in Long-Lasting, Safe Flooring for Your Kitchen
Your kitchen floors need to handle the heat, moisture, and heavy traffic of a busy commercial environment. Cementitious urethane is one of the best flooring options for durability, safety, and hygiene compliance. Don’t wait until cracks, slips, or health code violations force expensive repairs—invest in the best flooring solution today.
Contact ACP for a free consultation and let’s get your kitchen floors built to last!
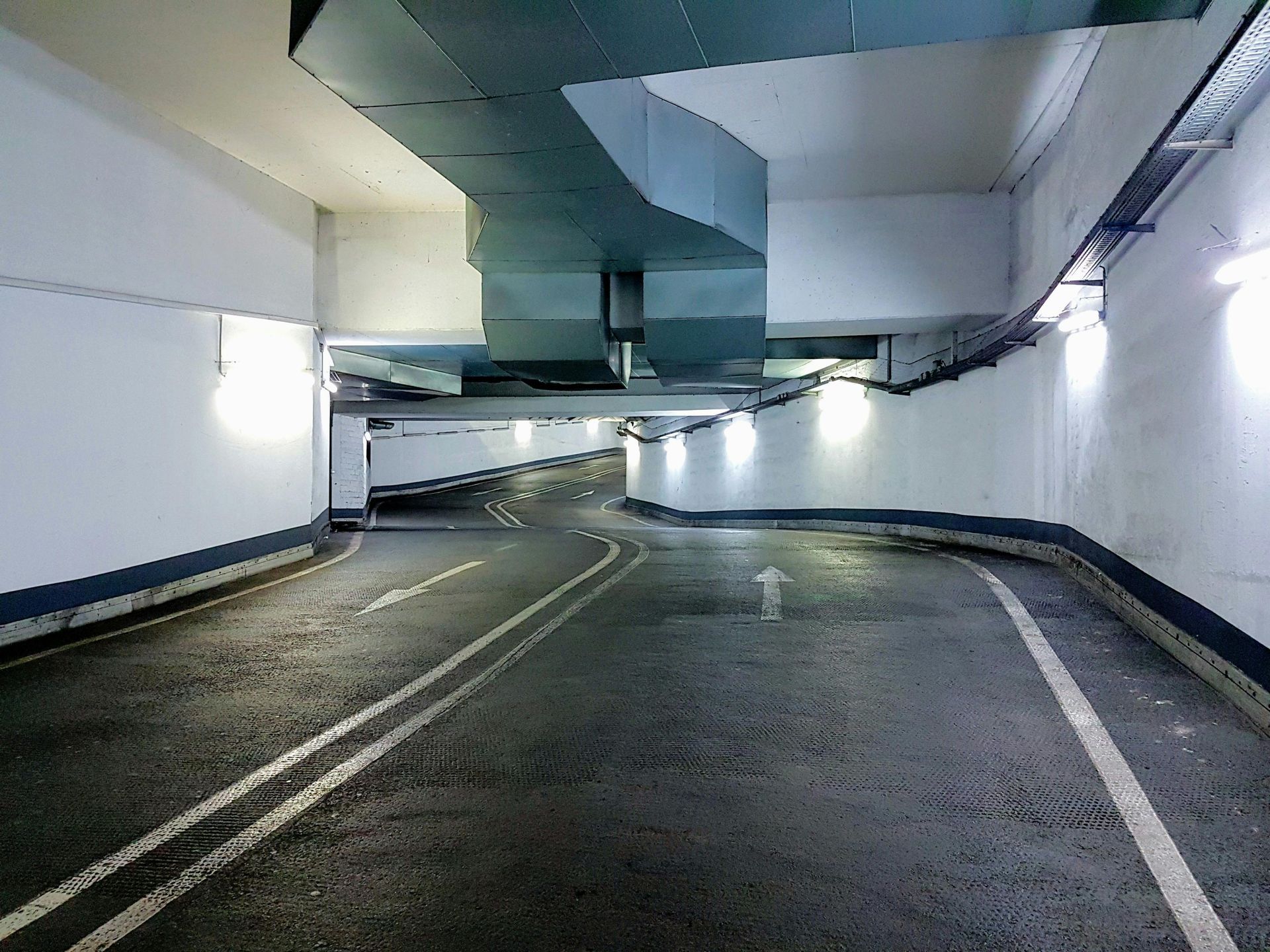